News
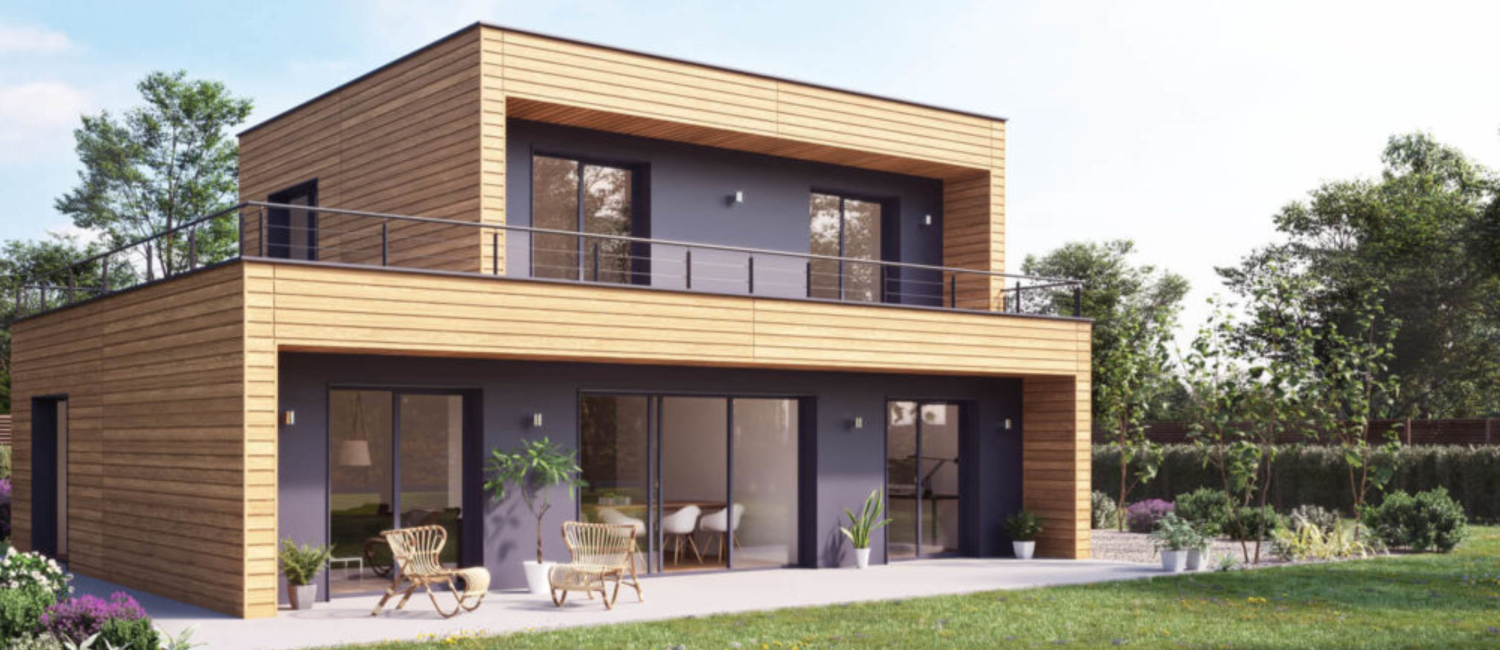
Hors-Site: A Promising Future for Sustainable Buildings
Discover the benefits of off-site construction and renovation, an approach that reduces CO2 emissions, optimizes costs and boosts productivity. Find out more about the opportunities and challenges from industry experts.
During the latest Build & Connect symposium, a captivating conference on off-site construction was held and presented by Frédéric Musselin, former Director of Business Development and New Construction Processes at Vivialis. This "fascinating subject" was discussed by three speakers: Bertrand Burger, Chairman of Burger & Cie, André de Chefdebien, Director of Innovation and Strategic Marketing, Rector Lesage Group, and Jean-Sébastien Lauffer, Technical Director, Techniwood. How can horsesite decarbonize tomorrow's buildings, and what are the advantages and drawbacks of this construction method? Find out more in a summary of the discussion.
Let's start with a reminder: hors-site is the workshop production of 2D or 3D - or modular - components, ready for assembly on site. One of the distinctive features of this construction method is that it adds value to the various factory-produced components. This is no mean feat at a time when costs, quality and carbon footprints in the construction industry all need to be improved. Today, off-site construction is being developed in many countries around the world, and has been booming in France for several years now, in both new-build and renovation projects, involving all building trades, from manufacturers to developers and builders.
The benefits of a practice on the rise
Horsesite construction offers many advantages over conventional construction, not only in terms of decarbonization, but also in terms of cost optimization, shorter lead times and increased productivity. For Frédéric Musselin, this construction method represents a "complete paradigm shift" and a "necessary evolution in the value chain" .
As Bertrand Burger explains, with off-site construction, the CO2 emission coefficient is divided by three compared with traditional construction methods. This factory-based approach also means that "production quality is much easier to manage than on building sites", with staff working in better conditions. The president of Burger & Cie stresses the meticulousness and attention to detail that come with working in a workshop, with professionals who are easier to train. André de Chefdebien, for his part, emphasizes the "flexibility" made possible by hors-site.
As far as aesthetics are concerned, there's no question about it, contrary to certain preconceived ideas. Jean-Sébastien Lauffer asserts: "You can make pretty things with prefabrication! Frédéric Musselin also confirms this idea during the discussion. In his view, prefabrication can result in "architecturally elaborate, personalized creations of surprising value and quality".
Another interesting point to note is that hors-site enables collaborative design, particularly between the architect and the main contractor, who go back and forth several times to ensure a coherent building structure.
And what about renovation?
With Techniwood, Jean-Sébastien Lauffer works mainly on off-site rehabilitation projects. Several feedbacks attest to the good performance of this system.
One of them concerns a project in Vigneux-sur-Seine, south of Paris. Techniwood was working on the renovation of 217 multi-family dwellings in 5 cross-connected buildings - hence the need to avoid nuisance between tenants. Another challenge was to remain on an occupied site for the duration of the project. As a result, all facades were installed without having to intervene inside the buildings. Prefabricated panels were installed using a crane, an extremely time-efficient procedure: in just one week, the two facades were completed! In 4 weeks, the entire site was completed, with minimal impact on the occupants.
Conditions for successful hors-site deployment
The first challenge is to raise awareness among all stakeholders. As Bertrand Burger affirms, "it is absolutely essential that all institutions - local authorities, government... - understand the interest" and promote this new construction method, particularly in France, where there is still some way to go. In Japan, for example, hors-site has existed since the post-war period and has endured ever since. Jean-Sébastien Lauffer is working towards this goal with Techniwood, reaching out to the various trades (architects, builders, design offices) to "bring all these players on board". The key is also to make the transition to these new ways of doing things without causing upheaval with negative effects. For André de Chefdebien, it is therefore necessary to "accompany the change" and monitor companies.
Another factor to consider is anticipation. " If we want hors-site to work, we have to make a design effort right from the start of the project", which today still stands in stark contrast to traditional practices in the construction industry, where people worry about the details of the work as it progresses.
In addition, to be fully virtuous, off-site construction must be accompanied by best practices such as the use of low-carbon materials, and the minimization of materials used. Digital technology is also a lever for "enabling the arrival of industrialized overmeasurement" (André Chefdebien).
As far as renovation is concerned, Jean-Sébastien Lauffer calls for a better understanding of the existing situation, with a more comprehensive information inventory - the "poor relation" of the hors-site, in his view, today.
Finally, it's not a question of "doing prefabrication for nothing", and using this construction method intelligently and when its added value makes sense, without resorting to it "at any price".
In this way, structures will be able to meet the various challenges posed by this new construction method: succeeding in being competitive in a fast-changing sector - particularly in terms of costs, appealing to customers and changing the traditionally mixed image of prefabricated construction, making the transition to digital uses such as BIM, finding quality workers, training in new skills and renewed uses... There are still many areas for progress, and by the same token, the promises and possibilities are immense.
A white paper is now available to find out more about hors-site best practice:
Les atouts de la construction hors-site : 7 propositions à destination des pouvoirs publics, by members of the Comité Stratégique de Filière "Industrie pour la Construction" working group.
No comment
Log in to post comment. Log in.